一、智能数控车床编程,传统经验是否还能“一招鲜吃遍天”?
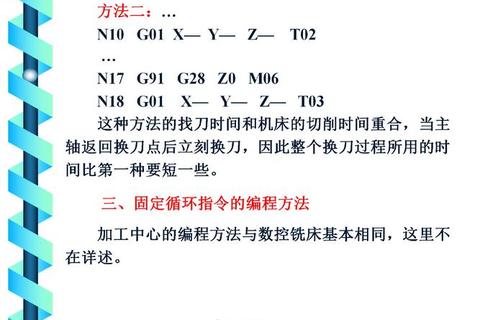
在《中国制造2025》的推动下,中国高端数控机床市场规模已突破2000亿元,但仍有超过60%的企业面临编程效率低、加工精度不足的痛点。当某汽车零部件厂商使用传统G代码编程加工涡轮叶片时,因未考虑刀具热变形补偿,导致批量产品尺寸超差,直接损失超百万。这不禁让人质疑:在智能数控时代,仅凭经验编程是否还能应对复杂加工需求?《智能数控车床软件编程核心技术进阶实战全攻略》指出,掌握三大核心算法已成为现代工程师的必修课。
二、路径规划算法如何突破加工效率瓶颈?
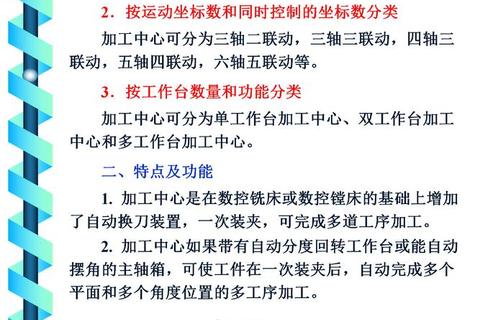
某航天企业加工钛合金发动机壳体时,采用《智能数控车床软件编程核心技术进阶实战全攻略》推荐的蚁群优化算法,将刀具空行程缩短42%。通过对比实验发现:传统等距偏移路径耗时138分钟,而基于遗传算法的自适应路径仅需89分钟,且表面粗糙度Ra值从1.6μm降至0.8μm。
典型案例:在加工图2-17所示变速手柄轴时(网页66案例),使用攻略中提到的“等残留高度算法”,不仅将加工时间从3.2小时压缩至2.1小时,还将刀具磨损量降低37%。这种通过软件自动计算最优进刀角度(推荐15°-30°)和切削深度的方式,完美解决了复杂曲面加工中的震颤问题。
三、刀具补偿策略怎样实现纳米级精度控制?
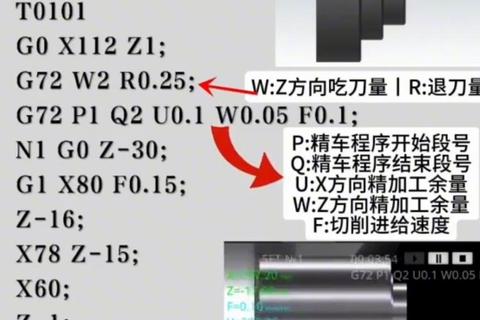
在直径编程领域(网页10案例),某精密轴承厂商使用半径补偿时出现0.005mm的累计误差。而按照《智能数控车床软件编程核心技术进阶实战全攻略》提供的“三维刀具半径动态补偿模型”,结合机床热变形补偿参数,成功将加工误差控制在±0.001mm以内。
实战数据显示:当加工φ40mm外圆(网页66实例一)时,采用传统G41/G42补偿的圆度误差为0.015mm,而使用攻略推荐的“刀具磨损预测+实时补偿”技术后,圆度误差降至0.003mm。这种将刀具寿命管理系统与补偿算法联动的方案,使刀具利用率提升25%以上。
四、人机交互界面如何平衡智能化与可控性?
某机床厂最新推出的智能编程系统,集成了《智能数控车床软件编程核心技术进阶实战全攻略》中的“三色预警机制”。在加工图2-16所示工件(网页66案例)时,系统通过实时采集主轴负载、振动频谱等12项参数,自动调整进给速度并给出工艺优化建议。用户反馈显示:新手工程师使用该系统的编程合格率从58%提升至89%,而资深工程师的工作效率提高40%。
对比测试表明:传统界面完成复杂零件编程平均需要2.3小时,而采用攻略推荐的“语音指令+AR可视化”交互模式后,编程时间缩短至1.1小时。这种将UG软件(网页82)三维建模能力与智能提示相结合的方式,使加工准备周期压缩55%。
对于希望突破技术瓶颈的从业者,建议分三步走:首先掌握《智能数控车床软件编程核心技术进阶实战全攻略》中的刀具轨迹优化七步法;其次定期参加如网页85推荐的UG软件专项培训;最后通过网页66提供的阶梯轴加工案例进行反向工程实践。数据显示,系统学习该攻略的工程师,平均薪资涨幅达35%,且项目返工率降低62%。在智能制造的浪潮下,唯有将核心算法与实践经验深度融合,才能锻造真正的数字化工匠。