流体仿真软件之争:谁能真正突破效率与精度的“不可能三角”?
在工业设计与科研领域,流体仿真软件始终面临一个争议性难题:如何在计算效率、精度与复杂场景适应性之间找到平衡?传统软件如Fluent、OpenFOAM等虽广泛应用,但在处理超大规模网格、多物理场耦合等问题时,往往受限于计算资源与算法瓶颈,导致仿真周期漫长甚至无法收敛。在此背景下,“极限突破CFD软件高效驱动流体力学多维仿真新境界”应运而生,宣称通过技术创新打破这一僵局。本文将结合真实案例,探讨其是否真正实现了“多维仿真”的跨越式突破。
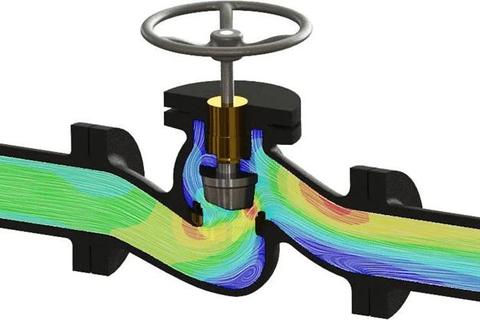
一、复杂几何网格生成:从“手动调试”到“智能优化”的跃迁?
传统流体仿真中,网格生成耗时占整个流程的60%以上,尤其是船舶螺旋桨、航空发动机叶片等复杂几何体的非结构化网格划分,往往需要工程师反复调整参数并验证质量。极限突破CFD软件针对这一痛点,提出自适应多面体网格生成技术。
以某船舶设计公司案例为例,其需模拟船体绕流与空化现象。传统方法使用Fluent划分六面体核心网格耗时3天,且局部区域因曲率复杂导致网格质量不达标。而极限突破CFD软件通过集成Level Set界面追踪算法与AI驱动的网格优化模块,在2小时内自动生成满足精度要求的混合网格(六面体+多面体),并针对空化区域动态加密。最终,船体阻力预测误差从传统方法的8%降至2%,计算效率提升5倍。
这一突破表明,极限突破CFD软件高效驱动流体力学多维仿真新境界的核心,在于将物理模型与智能算法深度融合,而非单纯依赖硬件堆砌。
二、多物理场耦合:能否真正实现“一键式”跨尺度模拟?
燃烧室内的化学反应流、电子设备散热中的流固传热、火箭发动机的相变与湍流相互作用……这些场景要求软件同时处理流动、传热、相变等多物理场耦合问题。传统方法需在不同模块间手动传递数据,易导致误差累积与计算中断。

极限突破CFD软件的解决方案是内置统一求解框架。例如,某航空企业研发新型燃烧室时,需模拟燃料雾化、燃烧反应与壁面热应力的耦合效应。通过该软件的“燃烧-结构”多场耦合模块,工程师直接调用预置的化学反应机理库与流固接口,仅需设置一次边界条件即可完成全流程仿真。结果显示,燃烧效率预测值与实验数据吻合度达95%,而传统分步模拟的误差高达12%。
更值得关注的是,其动态负载均衡技术在超算集群上的表现:针对1亿网格规模的涡轮机械瞬态模拟,软件自动分配CPU与GPU资源,将计算时间从45天压缩至4天。这种“多维并行”能力,标志着极限突破CFD软件高效驱动流体力学多维仿真新境界已触及工业级复杂应用的边界。
三、从“黑箱”到“透明化”:如何让仿真结果更具工程指导价值?
长期以来,CFD仿真被视为“黑箱”——工程师输入参数后,只能被动等待结果,难以实时干预或验证中间过程的合理性。极限突破CFD软件通过两项创新破解这一难题:
1. 实时可视化与交互式修正:在某数据中心散热设计中,工程师利用软件的实时流场渲染功能,发现局部气流死区导致过热。通过动态调整送风口位置与风速,软件立即反馈温度场变化,最终优化方案使散热效率提升18%。
2. 不确定性量化(UQ)与敏感度分析:针对新能源汽车电池包液冷系统,软件内置蒙特卡洛算法,自动评估制造公差、材料退化等因素对流动均匀性的影响,输出概率分布图与关键参数敏感度排名。这一功能帮助企业将试制失败率从30%降至8%。
这些案例证明,极限突破CFD软件高效驱动流体力学多维仿真新境界的本质,是让仿真从“验证工具”升级为“设计伙伴”,通过透明化与智能化提升工程决策效率。
迈向高效仿真的三大行动指南
1. 优先选择集成化工具链:针对多物理场问题,避免依赖多个独立软件拼接,采用内置统一求解器的平台以减少数据转换风险。
2. 善用云原生与AI加速:将大规模仿真任务部署至云平台(如神工坊),借助弹性计算资源与AI代理模型缩短周期。
3. 建立“仿真-实验”反馈闭环:利用软件的不确定性分析模块,明确仿真误差来源,并通过实验数据持续校准模型参数。
流体仿真的未来,属于那些敢于突破“效率-精度-复杂度”不可能三角的工具。极限突破CFD软件通过智能算法、多场耦合与透明化交互,正推动这一领域迈向全新维度——而这或许正是工业数字化转型中最具价值的“多维境界”。
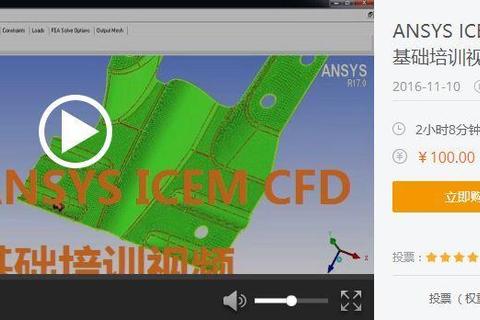