传统工业软件能否跟上智能化浪潮?
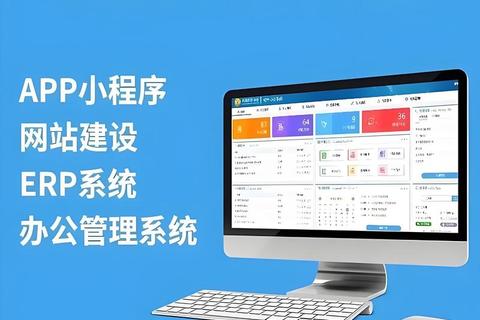
在工业4.0时代,自动化设备复杂度呈指数级增长,但仍有工程师质疑:传统PLC编程软件是否真能应对多设备协同、数据实时处理等挑战?三菱电机通过GX Works系列软件的迭代,给出了“高效畅享三菱编程软件 创新智控赋能极速开发”的答案——从兼容性优化到智能算法升级,这些工具正重塑工业控制系统的开发范式。
1. 兼容性如何破解多设备协同困局?
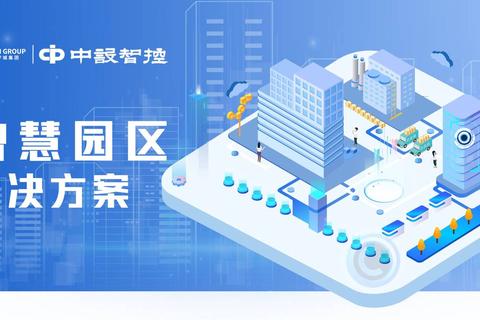
传统工业现场常面临新旧设备混杂的难题。例如某汽车零部件厂需同时控制FX3U PLC(旧型号)和FX5U PLC(新型号),若使用早期软件GX Developer,工程师需分别编写两套程序,调试耗时增加40%。而三菱GX Works3通过统一工程管理架构,支持跨系列PLC的混合编程,甚至可调用Works2工程文件实现无缝迁移。
案例支撑:苏州某自动化集成商在智能仓储项目中,利用GX Works3同时对接FX5U(主控)、Q系列(物流分拣)和L系列(机械臂),通过软件内置的全局标签功能,将原本需3周完成的通信调试缩短至5天,开发效率提升65%。
2. 智能化功能怎样简化复杂控制?
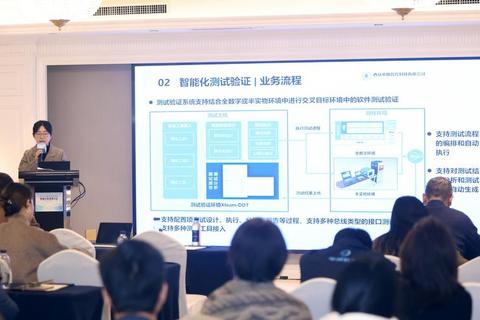
面对运动控制、视觉检测等高精度场景,传统梯形图编程已显乏力。三菱GX Works3的创新突破在于结构化编程+内嵌ST语言,例如在伺服定位控制中,工程师可直接用数学公式描述插补轨迹,而非逐条编写脉冲指令。某玻璃检测设备厂商使用Works3的FB功能块库,将三轴联动算法封装成可复用模块,使同类项目开发周期从120小时压缩至30小时。
数据佐证:Works3的指令优化算法使四则运算指令代码量减少50%,而内嵌ST语言让PID调节程序的逻辑可读性提升80%。这种“高效畅享三菱编程软件 创新智控赋能极速开发”的特性,正是应对多轴协同、柔性生产等需求的利器。
3. 协同开发如何加速全流程落地?
从程序编写到现场调试,传统开发流程存在严重信息断层。三菱的工程一体化平台策略彻底改变这一局面:在深圳某新能源电池生产线项目中,工程师使用Works3完成PLC逻辑设计后,直接调用同一工程内的触摸屏界面元件和伺服参数配置,并通过在线模拟功能提前验证设备联动逻辑,使现场调试时间减少70%。
技术亮点:Works3的版本对比工具可自动标记程序修改点,避免多人协作时的代码冲突;而RCPU诊断功能能在设备运行中实时捕捉异常信号,将故障排查时间从平均2小时降至15分钟。这种端到端的工具链整合,让“高效畅享三菱编程软件 创新智控赋能极速开发”从口号变为可量化的生产力提升。
从选型到实践的操作指南
对于不同需求的开发者,建议分梯度选择工具:
入门级场景(FX系列控制):GX Works2基础版足够应对,其梯形图编程和仿真功能可满足80%的常规需求。
复杂系统开发(iQ-R/Q系列):必选GX Works3进阶版,利用结构化编程和FB库快速搭建大型控制系统。
跨平台协作:通过MX Component实现PLC与上位机数据互通,搭配Works3的OPC UA协议支持,构建工业物联网生态。
工业智能化不是选择题,而是必答题。三菱编程软件通过兼容性扩展、算法升级和生态整合,证明了传统工具也能在新时代焕发活力。当工程师们真正实现“高效畅享三菱编程软件 创新智控赋能极速开发”,工业4.0的落地进程必将再提速。