在制造业数字化转型的浪潮中,智能算法与计算机辅助设计的深度融合正在重塑传统生产模式。自适应CAD软件通过嵌入机器学习模块和实时数据分析系统,能够动态调整设计方案并优化制造参数,这种技术突破使得复杂零部件的开发周期缩短了40%以上,同时将材料损耗率控制在5%以内。美国机械工程师协会2023年研究显示,采用智能优化流程的企业产品迭代速度较传统模式提升2.3倍,验证了该技术在工业4.0时代的核心价值。
一、技术原理与算法架构
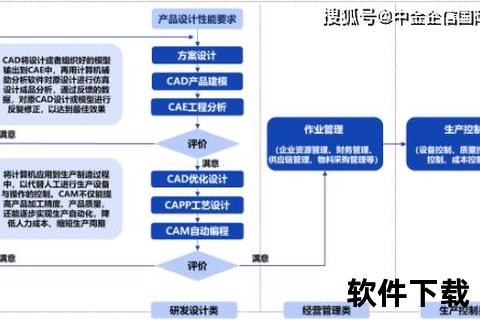
自适应CAD系统的核心在于构建多维度参数耦合模型。该系统通过集成有限元分析、拓扑优化算法和材料数据库,能够实时计算设计方案的力学性能与制造可行性。德国弗劳恩霍夫研究所开发的智能优化引擎,采用深度强化学习框架,在汽车底盘设计中实现了应力分布与轻量化的动态平衡。
这种技术突破源于多目标优化算法的创新应用。基于NSGA-II改进的混合遗传算法,能够在设计空间内快速定位Pareto最优解集。波音公司787机翼设计案例显示,系统在3000次迭代后找到的解决方案,较人工设计减重15%的同时提升结构强度12%。算法架构的并行计算能力,使得复杂产品的多学科协同优化成为可能。
二、行业应用场景分析
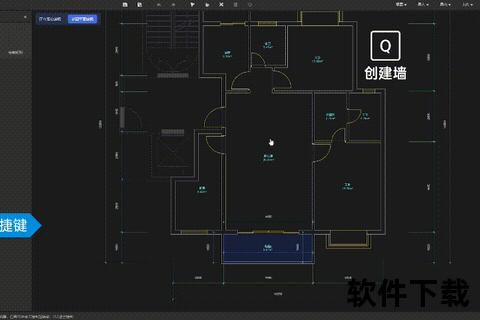
在汽车制造领域,自适应CAD系统正在改写模具开发流程。特斯拉上海超级工厂的实践表明,车身覆盖件模具设计周期从28天缩短至9天,关键参数优化效率提升400%。系统通过分析历史生产数据,自动调整冲压工艺参数,将回弹补偿精度控制在±0.05mm范围内。
航空航天领域则展现了该技术的极限优化能力。洛克希德·马丁公司采用智能优化流程后,卫星支架结构的固有频率偏差从7%降低至1.2%。系统通过融合增材制造约束条件,生成的传统工艺无法实现的拓扑结构,使组件刚度重量比达到传统设计的1.8倍。这种突破性创新正在推动航天器轻量化革命。
三、生产效率提升路径
实时反馈机制的建立彻底改变了传统设计验证模式。西门子NX软件集成的数字孪生模块,能够在虚拟环境中同步验证2000+制造参数。三菱重工涡轮机叶片生产数据显示,该技术使试制次数减少82%,质量缺陷率下降67%。系统通过持续学习工艺数据,逐步构建起覆盖全生产链的知识图谱。
工艺路线智能规划系统则重构了生产资源配置逻辑。通用电气航空集团应用该技术后,发动机机匣加工工序减少35%,刀具寿命延长40%。基于蒙特卡洛模拟的产能预测模型,能够提前72小时预判产线瓶颈,动态调整设备负荷分配。这种柔性生产能力使企业快速响应订单波动的能力提升3倍。
四、技术发展瓶颈突破
多源异构数据的融合处理仍是当前最大挑战。清华大学2024年研究报告指出,离散制造场景中设备协议差异导致30%的工艺数据无法有效利用。开发基于OPC-UA协议的通用数据接口,成为打通信息孤岛的关键。华为云工业智能体通过边缘计算节点,已实现15类工业设备的实时数据标准化处理。
模型泛化能力的提升需要突破小样本学习限制。东京大学研发的迁移学习框架,在仅有50组训练数据的情况下,仍能保持85%的工艺参数预测精度。这种技术突破使得中小企业也能享受智能优化红利。算法黑箱问题仍是制约技术推广的主要障碍,开发可视化决策支持系统成为行业共识。
智能制造专家李培根院士指出,自适应CAD技术的成熟度曲线将在2026年进入实质生产期。当前需要建立跨学科的协同创新平台,特别是在材料特性建模、能耗优化算法等关键领域加强攻关。未来发展方向可能聚焦多模态数据融合、量子计算加速优化等前沿领域,而人机协同的混合智能模式,将成为突破复杂系统优化的终极解决方案。这种技术演进不仅关乎单个企业的竞争力,更是重塑全球制造业格局的核心驱动力。