当传统制造业遭遇数字洪流:是颠覆还是重生?
过去十年,全球制造业经历了从“流水线轰鸣”到“数据无声奔涌”的剧变。一边是德国工业4.0、美国工业互联网的强势崛起,另一边是大量工厂仍在为设备联网率不足20%而挣扎。这场变革中,一个关键争议浮出水面:高效能智慧化驱动制造业软件是否真能成为传统工厂的“救命稻草”?
让我们看一组对比:2023年我国工业互联网核心产业规模突破1.3万亿元,但规上工业企业数字化转型比例仅为19%。这种冰火两重天的格局,正是制造业数字化转型最真实的写照。当机器视觉开始替代质检员的眼睛,当算法指挥着千万台设备协同生产,传统制造业的生存法则正在被彻底改写。
1. 数据孤岛如何打破?智能决策系统给出答案
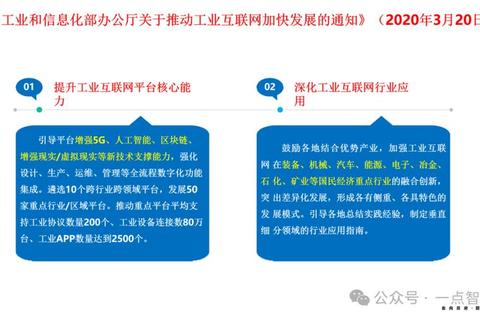
在广东惠州,雷曼光电的Micro LED显示屏生产线上,200余台设备实时传输着13类工艺参数。通过部署智能决策系统,企业将产品缺陷率从0.8%降至0.3%,设备综合效率(OEE)提升26%。这背后,正是高效能智慧化驱动制造业软件在发挥作用。
徐工集团的转型更具代表性。其混凝土机械板块通过搭建工业大数据平台,将研发周期缩短30%,售后故障处理响应时间从48小时压缩至4小时。核心秘诀在于:将分布在23个系统的数据打通,构建起涵盖供应链、生产、服务的全链条数字孪生。
这些案例揭示了一个真理:数据不是负担,而是新石油。当企业学会用智能算法提炼数据价值,就能实现从“经验驱动”到“模型驱动”的质变。根据国家工业信息安全发展研究中心数据,2022年我国工业设备上云率已达17.7%,边云协同普及率同比提升5.5个百分点,这为智能决策提供了坚实基础。
2. 柔性生产能否实现?工业互联网平台正在破局
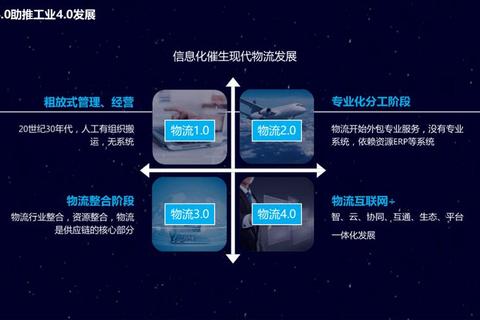
江苏永祺车业的车间里,每天要处理300多种自行车零部件的组合。通过部署柔性制造系统,企业将订单交付周期从45天缩短至7天,库存周转率提升40%。其核心在于:将ERP、MES、WMS系统深度整合,构建起动态响应的生产网络。
更令人惊叹的是亚马逊AWS与西门子的合作案例。通过工业物联网平台,双方实现了全球45家工厂的产能动态调配。当北美工厂遭遇供应链中断时,系统自动将订单分流至亚洲工厂,全程无需人工干预。这种“数字韧性”,正是高效能智慧化驱动制造业软件赋予的新能力。
这类转型已非个案。2023年我国跨行业工业互联网平台达50家,较2020年增长3倍,形成覆盖电子、机械、化工等80余个细分领域的服务矩阵。当平台能像“乐高积木”般灵活组合,传统的大规模标准化生产模式,正在向小批量定制化方向演进。
3. 产业链协同怎样升级?云端生态重塑制造格局

上海云汉芯城的实践颇具启示。这个电子元器件B2B平台,通过数字化供应链系统,将中小企业的采购周期从7天压缩至4小时。更关键的是,其国产芯片搜索引擎已积累60万条替代关系数据,助力800余家国内芯片厂商打开市场。
在广东江门,推行的“链式改造”策略成效显著。通过将五金卫浴产业链的200余家企业接入工业互联网平台,整体采购成本降低12%,协同设计效率提升35%。这种“产业集群数字化”模式,正在改写“单打独斗”的转型逻辑。
这些变革的背后,是产业协同逻辑的根本转变。据《全国工业互联网平台应用数据地图》显示,2022年供应链管理云化在电子行业渗透率达46.1%,研发设计云化在交通设备制造业达到22.3%。当产业链上下游能在数字空间无缝对接,传统的地理集聚优势,正在被数据连接能力重新定义。
穿越转型迷雾的三大行动指南
面对这场制造业的“数字长征”,企业需要更务实的策略:
1. 阶梯式推进:从设备联网(17.7%的已上云设备是起点)、数据治理,逐步扩展到智能决策,避免“一步到位”的冒进。
2. 生态化协同:加入行业级工业互联网平台,善用提供的诊断服务(如江门1906家规上企业的转型经验),降低试错成本。
3. 人才双轨制:既引进算法工程师,也通过“移动云课堂”等工具提升一线员工数字素养,破解“懂技术的不懂工艺”困局。
这场由高效能智慧化驱动制造业软件引领的数字化转型新浪潮,本质是制造业认知革命。它不是简单的机器换人,而是通过数据流重构价值流,用算法重新定义制造逻辑。那些率先完成“数字基因”改造的企业,正在将转型阵痛转化为竞争优势,而这或许就是中国制造迈向高质量发展的必由之路。