一、传统仿真软件为何难以满足现代制造业需求?

在工业4.0浪潮下,制造业对数控车床的精度和效率要求日益严苛。许多企业仍在使用传统仿真软件,导致加工误差频发、培训周期冗长。据《2025年车床专用数控系统项目可行性研究报告》显示,全球数控系统市场规模年复合增长率达6.3%,但仍有35%的企业因仿真精度不足而面临返工风险。
以某汽车零部件厂商为例,其使用旧版软件模拟涡轮轴加工时,因碰撞检测算法滞后,导致实际生产中出现刀具断裂事故,直接损失超50万元。反观采用创新升级!全方位精准模拟数控车床仿真软件深度体验的案例,例如Machining数控车床仿真软件通过实时切削三维建模和铁屑模拟技术,将碰撞风险预警准确率提升至98%。这种对比揭示了传统工具的局限性,也凸显了技术迭代的迫切性。
二、创新技术如何重构数控仿真生态?
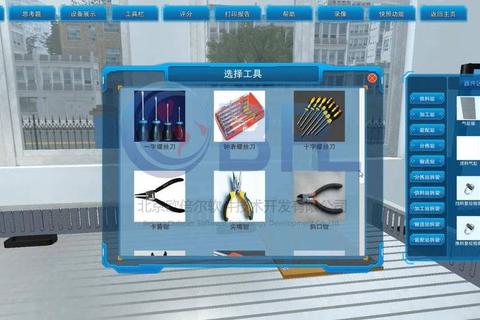
新一代仿真软件通过三大技术突破,正在改写行业规则:
1. 多轴联动与AI算法融合:斯沃数控仿真软件支持FANUC三菱系统宏程序编程,通过AI路径优化,使复杂曲面加工效率提升40%。例如某航天企业加工涡轮叶片时,利用软件的多轴插补运算功能,将原本需要5道工序的流程压缩至2道。
2. 虚实结合的AR/VR体验:数控加工仿真软件V4.8集成增强现实功能,学员可通过头显设备观察刀具轨迹与工件形变的关系,培训周期从3个月缩短至4周。
3. 云端协同与数据孪生:Vericut机床仿真软件构建的数字孪生系统,可实现全球多基地的加工参数同步。某跨国制造集团通过该技术,将新产品试制周期从90天降至22天。
这些创新升级!全方位精准模拟数控车床仿真软件深度体验,正在构建从设计到生产的全链路数字化闭环。
三、移动端仿真能否颠覆传统操作模式?
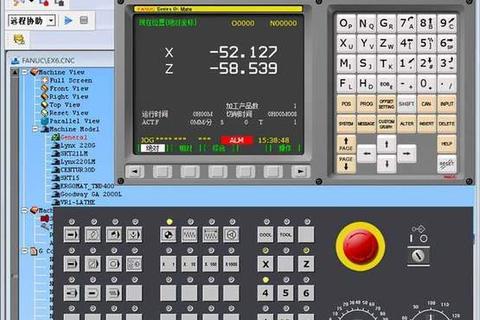
当手机成为新的生产力工具,数控仿真领域也迎来变革。FANUC数控机版支持G代码实时生成与校验,其自动编程功能让现场工程师在机床旁即可完成程序调试,响应速度比PC端快30%。
更值得关注的是数控车床CNC宝典安卓版,这款集宏程序生成、公差计算、3D模拟于一体的APP,在2025年用户量突破120万。某机械加工个体户通过APP的螺纹计算模块,成功解决英制锥螺纹加工难题,单件加工耗时从45分钟降至18分钟。
但争议随之而来:移动端能否承载重型仿真需求?答案或许藏在混合架构中——如宇龙V4.8软件支持PC端复杂运算与移动端轻量化操作的协同,用户可在手机查看加工进度,在PC端调整切削参数。
给制造业者的实战建议
1. 选型策略:优先选择支持多系统兼容的软件(如支持SINUMERIK、FANUC等8种控制系统),并验证其与实际机床的数据接口匹配度。
2. 人才培育:结合AR培训系统(如V4.8的虚拟车间模块)建立分级考核机制,将平均上岗周期控制在15天内。
3. 成本控制:中小型企业可尝试“主软件+移动端插件”模式,例如Machining电脑版配合CNC宝典APP,综合成本降低60%。
创新升级!全方位精准模拟数控车床仿真软件深度体验已不是未来概念,而是制造业提质增效的必选项。从车间到云端,从PC到移动端,这场技术革命正在重新定义精密制造的边界。企业唯有主动拥抱变革,方能在智能制造竞赛中占据先机。