家具行业大变革:拆单软件如何改写智造规则?
传统家具行业正面临一个尴尬的困境:一边是消费者对定制化需求的井喷式增长,另一边却是人工拆单效率低下、错误频发的生产瓶颈。安徽新鑫家曾为此付出沉重代价——每月因设计图纸与生产数据不匹配导致的板材浪费高达20%,而拆单员加班加点仍难跟上订单增速。这种矛盾如何破解?智能高效革新升级 家具拆单软件驱动智造未来的答案,正在重塑行业格局。
一、拆单软件如何实现效率飞跃?
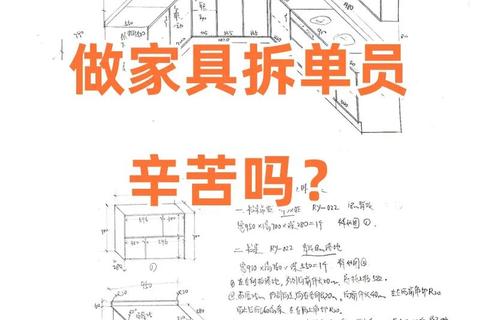
过去,家具企业依赖设计师手工绘制CAD图纸,再交由拆单员逐项分解板材尺寸、孔位数据。这种模式不仅耗时,还容易因沟通误差导致生产事故。安徽新鑫家的转型案例极具代表性:2022年引入酷家乐智造通后,其拆单效率提升3倍,1名员工单日处理订单量从2套跃升至6套,错误率降低20%。
拆单软件的效率密码在于两大核心能力。
一是参数化建模。以晨丰软件为例,设计师在WebCAD平台调用模块化柜体模板,通过拖拽、尺寸调整即可生成三维模型,系统自动解析板材用量、五金配件清单,甚至生成设备识别的NC代码。这种“设计即拆单”的模式,让原本需要3天的手工流程缩短至2小时。
二是智能纠错。三维家DMS系统内置2000余项工艺规则,可自动检测孔位冲突、板材承重等隐患。某广州家具厂使用后,因设计不合理导致的返工率从15%降至3%。
效率提升的直接结果是成本优化。据行业测算,拆单环节每减少1天周期,企业流动资金周转率可提升5%-8%。
二、设计生产一体化是未来趋势吗?
传统生产链上,设计、拆单、制造环节犹如“信息孤岛”——设计师用酷家乐渲染效果图,工厂却要用2020Design重新建模,这种断层导致欧派门店需同时操作4套系统,人力成本增加30%。而智能高效革新升级 家具拆单软件驱动智造未来的关键突破,正是打破数据壁垒。
典型案例是博士家居的数字化实践。其通过三维家系统实现“方案直通车间”:消费者在门店的VR设计中调整柜门纹理,数据实时同步至工厂MES系统,自动触发板材切割指令。这种前后端一体化模式,使订单交付周期从45天压缩至25天。
更深层的价值在于数据资产沉淀。欧派家居的WCC智能拆单系统,累计存储超过100万套设计方案,形成涵盖8大品类、200种工艺的数据库。当新订单匹配历史方案相似度达80%时,系统自动推荐优化参数,使设计效率提升40%。这种数据驱动模式,让企业从“经验决策”转向“算法决策”。
三、智能制造需要怎样的技术支撑?
行业龙头企业的探索揭示了一个真相:拆单软件不是孤立工具,而是智能工厂的“神经中枢”。德国豪迈集团的CENTATEQ P-110设备印证了这一点——当拆单数据导入后,机床自动切换刀具,机器人完成板材上料,全程无人干预。该方案使某浙江家具厂的板材利用率从78%提升至92%,残次品率降至0.5%。
三大技术正在深度融合:
物联网协同:HOMAG的FEEDBOT机器人通过5G网络接收拆单指令,实现24小时不间断供料,设备综合效率(OEE)提升至85%;
AI工艺优化:数夫软件的智能排产算法,可根据订单紧急度、板材库存、设备负载等变量,动态调整生产队列,使设备闲置率降低25%;
云端部署:圆方FDM20平台支持万人在线协作,疫情期间助力200余家中小企业实现远程拆单,订单处理量逆势增长18%。
这些技术堆叠出的不仅是效率,更是柔性制造能力。某儿童家具企业通过云端拆单系统,将非标订单比例从30%提升至70%,毛利率增加12个百分点。
破局之道:企业如何拥抱智能拆单?
面对行业洗牌,中小企业的生存法则在于三步走策略:
1. 选型匹配:10人以下工厂可优先试用云承、阿尔法等轻量级软件,年产能超5000万的企业则需部署三维家DMS等工业级系统;
2. 人才升级:建立“软件操作+工艺知识”双轨培训体系,如某东莞企业通过内部认证机制,使拆单员人均产值从8万/月提升至15万/月;
3. 生态整合:打通ERP、MES系统数据接口,例如索菲亚通过PLM平台集成6类软件,实现从设计到安装的全流程追溯。
智能高效革新升级 家具拆单软件驱动智造未来已不是选择题,而是生存战。正如家居巨头欧派所言:“未来5年,不会用数据说话的企业,连参与竞争的入场券都拿不到。”当拆单软件从工具进化为生产力引擎,谁能抢占技术高地,谁就能在定制化浪潮中劈波斩浪。