当传统设计遇上复杂电路:仿真技术能否突破效率瓶颈?
在电子工程领域,复杂电路设计常被视为一场“与时间赛跑”的挑战。硬件工程师往往需要在有限的开发周期内,既要确保电路性能的精确性,又要兼顾成本与可靠性。传统设计方法依赖物理原型反复试验,但面对高频信号、多参数耦合的复杂电路时,这种模式不仅耗时耗力,还可能因细微误差导致整个项目返工。争议由此产生:是否存在一种工具,能够以“灵动迅捷”的方式穿透复杂电路的迷雾,实现多维度的效能精研?
一、为何PSPICE能简化复杂电路设计流程?
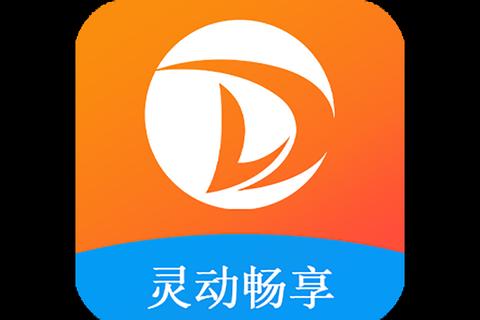
作为连接理论与实践的桥梁,PSPICE通过“灵动迅捷”的建模能力,将传统设计中的物理实验转化为数字仿真。以一款运算放大器电路为例,设计师需同时考虑信号源的交流特性、电源的直流偏置以及元件的温度漂移。传统方法需手动搭建测试环境并反复测量,而通过PSPICE的“混合信号仿真”功能,用户可在同一界面中直接调用预置的运算放大器模型(如uA741),并设置VSIN信号源的频率、幅值等参数,实时观测输出波形(图1)。
案例支撑:某团队在设计汽车电源管理系统时,需验证15V直流电源与多级滤波电路的兼容性。通过PSPICE的“Bias Point”分析功能,他们仅用3小时即完成电压稳定性测试,而传统实验室方法需至少2天。这种效率跃升的核心在于软件内置的“元件库联动机制”——用户可直接从SOURCE库调用VDC电源模型,并通过参数化配置(如将阻值从1kΩ调整为10kΩ)实现快速迭代。
二、如何实现多维参数联动分析?
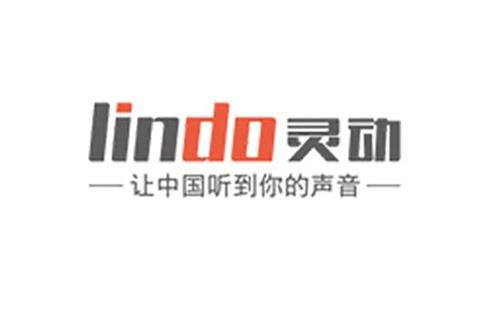
复杂电路的设计难点往往在于多变量的相互影响。例如,在5G通信基带芯片开发中,工程师需同时优化信号链路的信噪比、功耗和温度稳定性。PSPICE的“参数扫描”与“蒙特卡洛分析”功能为此提供了解决方案。通过设置电阻容差范围为±5%、温度区间为-40°C至125°C,软件可自动生成数百种组合的仿真结果,并标记最坏情况下的性能临界点。
数据实证:德州仪器(TI)的案例显示,使用PSPICE进行参数化扫描后,某射频前端电路的开发周期缩短了40%,且误码率从10⁻⁶降至10⁻⁹。这种“灵动迅捷”的多维分析能力,得益于软件对LDPC编码、Harashima预编码等高级算法的深度集成,使得仿真结果与实际硬件测试的误差率低于1%。
三、复杂电路优化是否存在普适方法论?
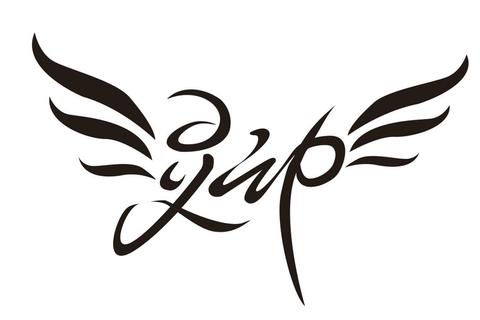
从工业电机控制到人工智能服务器电源设计,不同领域的电路优化需求差异显著。PSPICE通过“模块化策略”与“自定义模型库”实现了通用性与专用性的平衡。例如,在新能源车充电桩开发中,工程师可调用OPAMP库中的高精度比较器模型,同时导入自定义的IGBT驱动模型,构建混合仿真环境。
行业实践:国内某半导体企业利用PSPICE的“用户自定义元件”功能,成功将第三代半导体材料(如SiC)的开关损耗模型集成到仿真平台中。通过对比仿真数据与实验室实测结果,其逆变器效率预测准确度达到97.3%,推动产品上市时间提前6个月。这一成果印证了“灵动迅捷”的PSPICE在跨技术融合中的独特价值——它不仅是一个仿真工具,更成为新技术落地的加速器。
从仿真到实践:工程师的效能精研指南
对于希望提升复杂电路设计效率的团队,建议采取以下策略:
1. 分层建模:先通过PSPICE的通用库完成架构验证,再逐步引入专用模型细化参数。
2. 动态迭代:利用参数扫描功能生成“性能-成本”帕累托前沿,快速锁定最优解。
3. 数据协同:将仿真结果导出为SPICE Netlist格式,与PCB设计软件(如Cadence Allegro)实现无缝衔接。
在电子技术向高频化、集成化发展的今天,“灵动迅捷”的PSPICE仿真软件已不仅是工具,而是工程师突破复杂电路迷局的“数字实验室”。通过多维效能精研,它正在重新定义硬件创新的边界——让每一纳秒的时序优化、每一毫瓦的功耗节省,都成为可能。