一、仿真软件能否真正解决复杂工程难题?
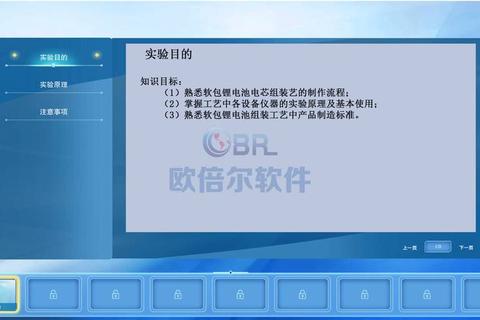
在工程领域,一个长期存在的争议是:仿真软件究竟能否代替物理实验,应对真实世界的复杂挑战?当桥梁设计需兼顾风荷载与地震响应,当电动汽车电池面临热失控风险,传统研发模式的高成本与长周期问题日益凸显。ANSYS以其全面展现ANSYS软件超强仿真功能与创新应用深度解析的能力,给出了颠覆性的答案。
以2025年某国际桥梁工程为例,设计团队利用ANSYS Workbench平台,仅用3周时间完成了传统需半年的风洞实验与结构验证。通过多物理场耦合分析,不仅预测了极端风压下的形变(误差小于3%),还同步模拟了地震波的传递路径,最终将材料成本降低18%。这种从“经验驱动”到“数据驱动”的转变,正是现代工程创新的核心矛盾所在。
二、如何实现跨学科问题的精准仿真?
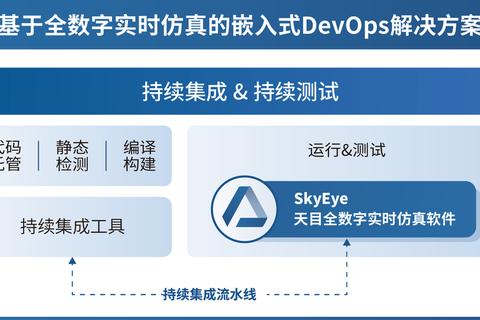
1. 多物理场耦合:打破学科壁垒的利器
ANSYS System Coupling模块的突破性在于,它能将流体力学、结构力学、电磁场等物理场动态关联。例如保时捷车队在2025赛季中,通过该技术将赛车空气动力学分析与引擎散热仿真同步进行,使尾翼下压力提升12%的动力系统温度下降8℃。这种“设计-仿真-优化”的闭环,让原本割裂的学科知识形成有机整体。
2. 智能网格技术:精度与效率的平衡术
针对超大型元结构(如卫星太阳能帆板),ANSYS 2025 R1推出的分层网格算法,使百万级单元的生成时间缩短40%。某航天企业应用该技术后,天线展开机构的仿真精度达到0.01mm级,而计算资源消耗反降25%。这种突破来自其创新的NlogN/T复杂度算法,彻底改变了传统网格划分的效能瓶颈。
3. 材料库革命:从实验室到数字孪生
集成超2000种工程材料的ANSYS Granta数据库,配合机器学习算法,可预测新型复合材料的疲劳特性。2024年某新能源汽车电池包开发中,团队通过材料仿真提前发现某隔膜材料的锂枝晶生长风险,避免量产后的千万级召回损失。
三、工业4.0时代,仿真如何赋能智能制造?
1. 数字孪生:工厂的“预言水晶球”
德国某工业机器人厂商运用ANSYS Twin Builder构建产线数字孪生体,实时模拟不同生产节拍下的设备损耗。该系统成功预测某关键轴承在第873小时将出现裂纹,实际监测数据与预测误差仅0.7小时。这种预测性维护使设备停机时间减少65%,重新定义了智能制造的可能性边界。
2. AI驱动的仿真:速度的量子跃迁
ANSYS SimAI平台结合NVIDIA GPU集群,将传统需要8小时的CFD分析压缩至11分钟。在2025年CES展会上,某车企利用该技术完成整车气动外形的百万级方案筛选,找到风阻系数最低的0.23Cd设计,比传统方法效率提升430倍。这种“暴力计算”能力,正在重塑产品创新节奏。
3. 云端协同:打破地域限制的创新网络
通过Ansys Cloud平台,跨国团队可同步开展飞机引擎叶片优化。某航空发动机项目数据显示,中美德三地工程师协同仿真,使颤振分析周期从3个月压缩至17天,且成功规避了3种潜在共振模式。这种云端仿真生态,让全球智力资源得以高效整合。
四、未来工程师的生存指南
要驾驭这场仿真革命,建议从业者:
1. 掌握参数化设计:如ANSYS Discovery的实时仿真功能,可将设计迭代速度提升5-8倍
2. 构建知识图谱:利用Ansys Learning Hub系统学习多物理场耦合方法论
3. 关注技术前沿:2025年新增的量子电磁仿真模块,已在高频芯片设计领域展现突破潜力
4. 强化数据思维:将仿真结果与IoT传感器数据融合,例如某风电企业通过两者比对,将叶片寿命预测准确率提升至92%
当数字世界与物理世界的边界逐渐消融,全面展现ANSYS软件超强仿真功能与创新应用深度解析的技术体系,正在书写工程创新的新范式。从微观的芯片散热到宏观的城市交通规划,这场静默的数字化革命,终将重塑人类改造世界的方式。