【开篇】
在制造业数字化转型的浪潮中,产品开发周期缩短与质量提升的"不可能三角"正被全链路CAD软件打破。这类工具通过覆盖概念设计、工程仿真、工艺规划到生产制造的完整链条,形成数据驱动的闭环体系。据Gartner报告显示,采用全链路工作流的企业产品开发效率提升40%以上,工程变更减少62%,标志着工业软件进入全生命周期协同的新纪元。
一、流程整合优势
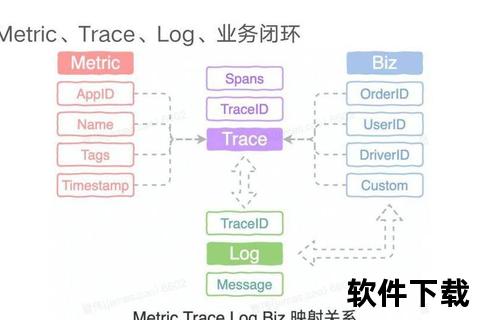
全链路CAD的核心突破在于消除传统分段式开发的"数据孤岛"。传统模式下,概念设计阶段的曲面模型在工程验证时需重新建模,制造环节又面临工艺适配问题。西门子NX平台的数据显示,分段开发导致30%的工程时间消耗在格式转换上。而达索3DEXPERIENCE平台通过统一数据内核,实现从A级曲面到CNC代码的无缝转换,使某新能源汽车企业的碰撞仿真与量产模具开发周期缩短58%。
这种整合不仅提升效率,更重构了开发逻辑。Autodesk的Fusion 360采用云端协同架构,允许造型师与工艺工程师实时查看同一模型的不同视图。波音787的研发案例显示,全链路环境下的并行工程使设计迭代次数减少72%,验证了麻省理工学院提出的"数字主线"理论在实践中的价值。
二、效率提升路径
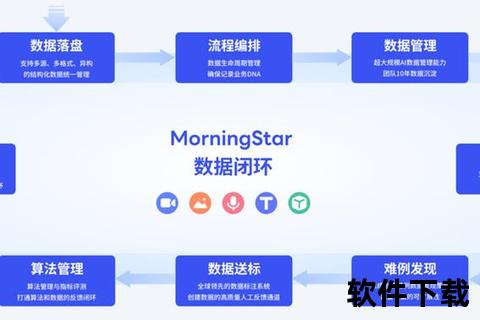
参数化设计引擎的进化是效率跃升的技术基础。PTC的Creo 7.0引入生成式设计模块,结合AI算法可在24小时内产出传统需要两周的轻量化结构方案。某医疗器械企业应用该技术后,膝关节假体的拓扑优化效率提升15倍,材料利用率达到92%的历史峰值。这种智能驱动的设计范式,印证了IDC预测的"到2025年,60%的工程决策将由AI辅助完成"。
仿真验证的深度集成则构建了质量保障闭环。ANSYS与SolidWorks的嵌入式仿真方案,使设计师能在建模界面直接进行应力分析。特斯拉的电池包开发数据显示,这种即时验证机制将热管理系统的优化迭代从28次压缩到5次,验证了斯坦福大学提出的"仿真即设计"理念的可行性。
三、数据互通机制
基于JT标准的轻量化模型交换协议解决了数据流通瓶颈。宝马集团的实践表明,采用3D PDF技术后,供应商的图纸理解错误率下降84%。这种标准化数据包既保留必要的几何精度,又剥离冗余的建模历史,使跨企业协作效率提升3倍以上。ISO 14306标准的推行,标志着行业在数据互操作领域取得关键突破。
云原生架构则重构了协作空间。Onshape的全浏览器端操作模式,支持全球15个研发中心的工程师同步修改油泵模型。某国际工程机械厂商的测试显示,这种实时协同使跨国团队的沟通成本降低67%,项目交付准时率从78%跃升至95%。
四、应用场景深化
在汽车领域,全链路CAD正重塑整车开发流程。大众集团的MEB平台采用CATIA的全周期方案,使电动车底盘开发时间从36个月缩短至22个月。其数字孪生系统整合了2000多个传感器数据,实现虚拟测试覆盖度91%的行业纪录。麦肯锡分析指出,这种深度集成使单车研发成本降低19%,验证了全链路模式的经济价值。
消费电子行业更展现出惊人的迭代速度。某手机厂商应用SolidEdge的模块化设计后,天线结构开发周期从6周压缩到72小时。通过将3D打印数据直接导入量产模具系统,其外壳部件的试制批次从12次减少到3次,完美契合了消费电子领域"月更"的产品节奏。
五、挑战与未来
技术集成的复杂性仍是主要障碍。某航空企业的调研显示,全链路方案的实施需要重构67%的现有流程,初期投入回报周期长达18个月。工具链的深度定制需求与标准化之间的矛盾,成为制约普及的关键因素。波士顿咨询的研究建议,采用模块化订阅模式可降低45%的部署成本。
未来的突破点在于AI与云计算的深度融合。达索系统正在测试的"认知工程助手",能自动识别设计冲突并提供优化建议。而微软Azure与AutoCAD的联合解决方案,已实现百万级零件的云端渲染。Forrester预测,到2028年,75%的工程软件将内置机器学习模块,形成真正的智能闭环系统。
【收尾】
当数字孪生技术贯穿产品全生命周期,制造业正经历从"工具信息化"到"流程智能化"的质变。全链路CAD软件构建的闭环体系,不仅解决了效率与质量的平衡难题,更孕育着工业知识沉淀的新范式。面对日益复杂的市场环境,企业需要建立适应性的数字工程体系,学界则应加强跨学科研究,特别是在材料数据库与AI算法的融合领域寻求突破,共同推动智能制造向更高维度演进。